WE shape the urban landscape - that includes every employee. Together and with joy and passion, we create appealing bricks for living spaces. These are the people behind the bricks:.
The preparation
"It's a bit like baking a cake - except that our measuring cups are excavator shovels." - Johann, Gerold, Geert and Marcin take care of the material supply in the processing department.
Everything begins with the extraction of the raw material . The lion's share of our clay currently comes from a clay pit that is only a stone's throw away from the company premises. We really do produce a local product! Other components are added to the clay to optimise the properties of the future brick. This "baking mixture" is then crushed and homogenised in the pan grinder, rollers and mixers. The finished prepared material is transported by wheel loaders onto conveyor belts and towards our presses, where the next team takes over.
The electricians
We employ a whole team of electricians. Our E-Team, consisting of Kjell, Tim, Berthold, Max, Jesko and Tom, is, if necessary, also on duty in the middle of the night, so that everything runs perfectly in the entire company.
And when we invite to big events, the men transform into our stage technicians, lighting technicians and DJs. A versatile team!
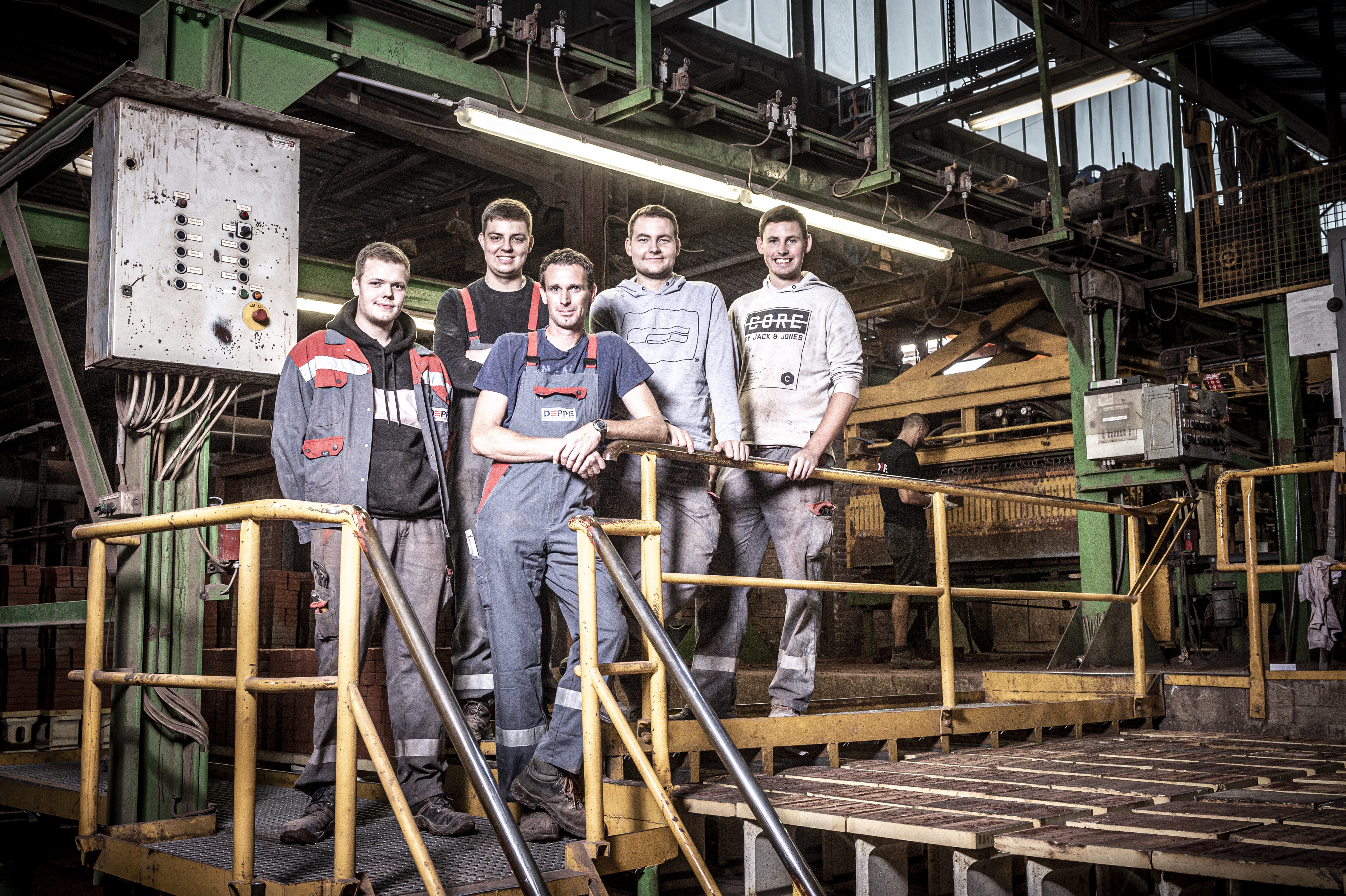
The presses
Torsten, Pietro and Jens operate our various presses and ensure that our bricks are in good "shape", whether they are hand-moulded, waterstruck or extruded bricks. They no longer have to put the clay bricks into the moulds by hand, modern machinery has taken over that part. But the principle remains the same: the clay is pressed into a mould. This results in surface marks that remain visible even after firing and give each brick its individual surface structure. The handcrafted outer appearance of the brick is preserved.
While sand ensures that the clay slides out of the mould in the hand-moulding process, water is used in the waterstruck process. Waterstruck bricks are therefore somewhat smoother than hand-moulded bricks. The extrusion process uses a different machine. Here, the clay is pressed into a long strand from which the raw bricks are cut off. This produces more homogeneous bricks than other manufacturing processes.
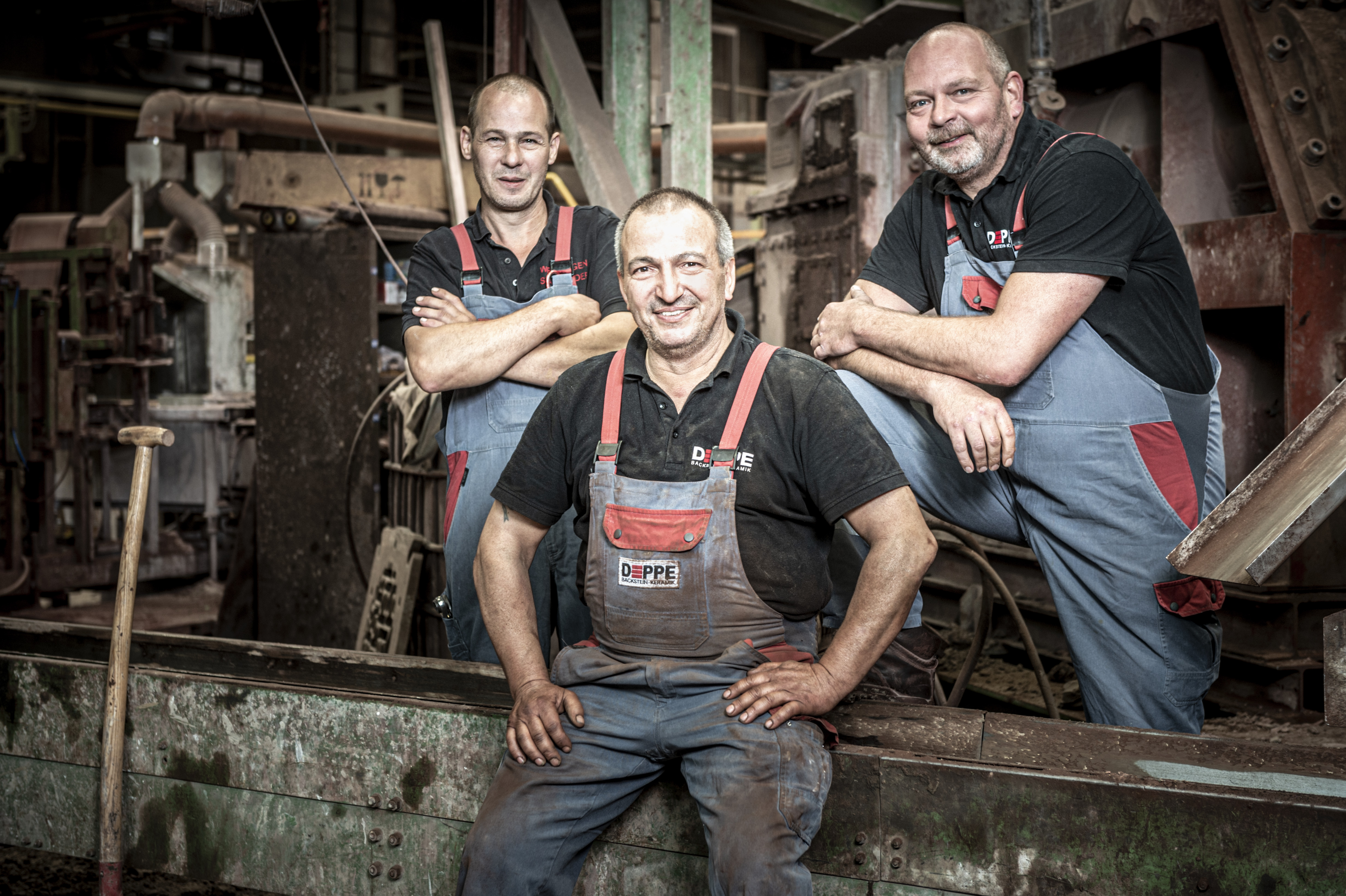
Technical management/Production management
Material is needed here, staff is there, there is a problem with one of the machines, the packaging system has to be readjusted, when will the new samples come out of the kiln, is the colour result of the new batch as desired, are all quality criteria fulfilled, are the kiln cars running, is everything perfectly timed perfectly ..., ..., ...?
Jürgen, Sascha, Evelyn and Hans keep track of all the processes together with the management. This includes production and personnel planning, monitoring of the ceramic processes, maintenance of the countless machines, material planning and a lot more.
We have invested a lot in the past years and have increased our production capacity as well as our staff. While Jürgen has been with us for over 30 years, engineers Hans, Sascha and Evelyn have joined us in the course of the last few years.

Sawing hall
Geert, Ibrahim and Daniel from the sawing hall wear the ear protection for a reason. Not every brick façade is built in the traditional way: the men here cut brick slips on impressive saws and the noise can be deafening. Slips are thin slabs of stone that are only 0.5 to 2.5 cm thick and are not laid but glued to the back brickwork.
Some of our special brick formats that vary from the standard shapes are also cut here.
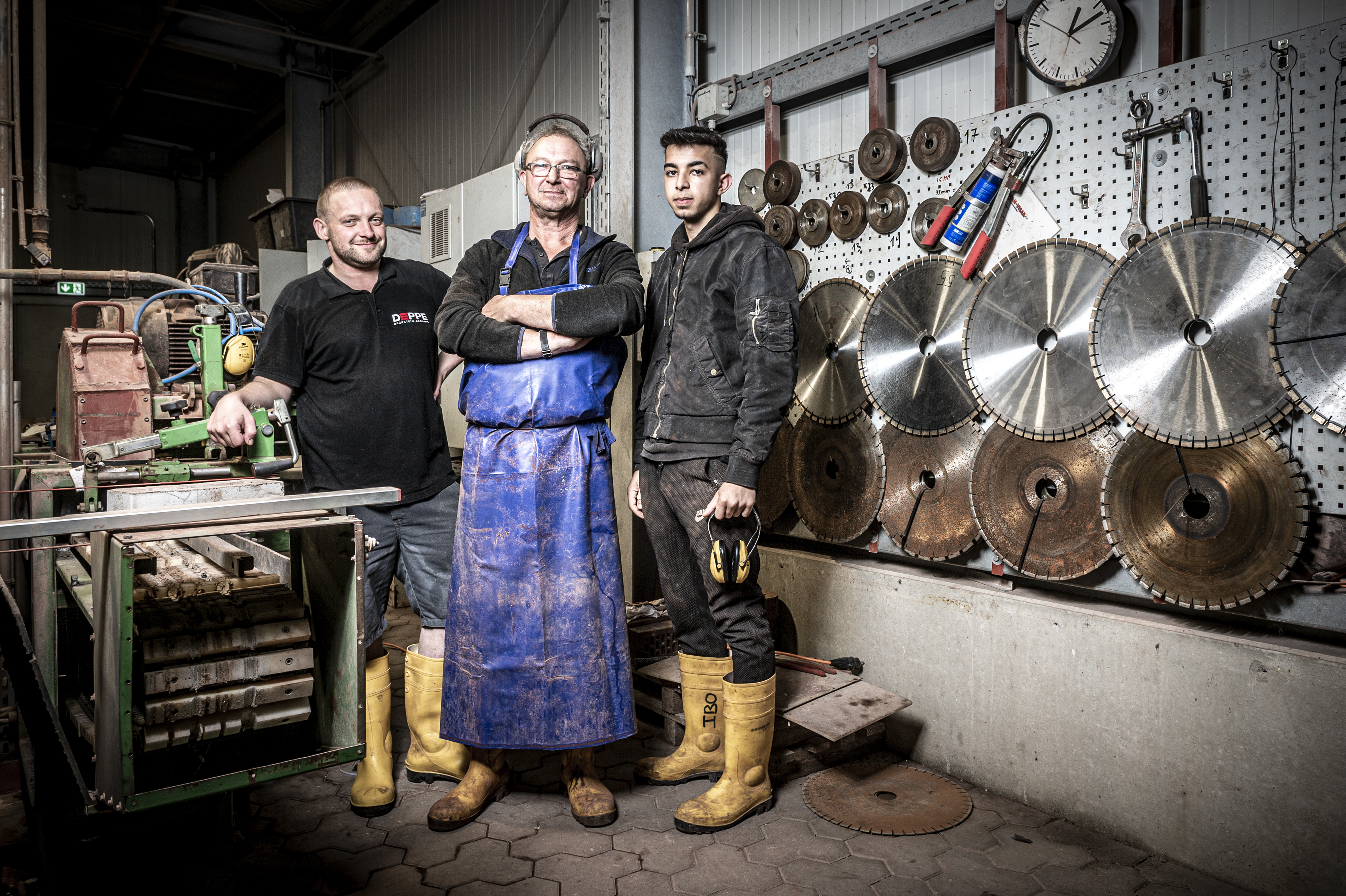
The mechanics
These are not the roadies of AC/DC but our locksmiths and mechanics. Roy, Chris, Salvatore, Daniel, Sascha, Henning, Siegfried and Tobias are not afraid to get their hands dirty, just like everyone else in the company.
If necessary, they are at work at 3 a.m., maintaining, repairing and ensuring that the tunnel kilns in particular, but also everything else, runs like clockwork.
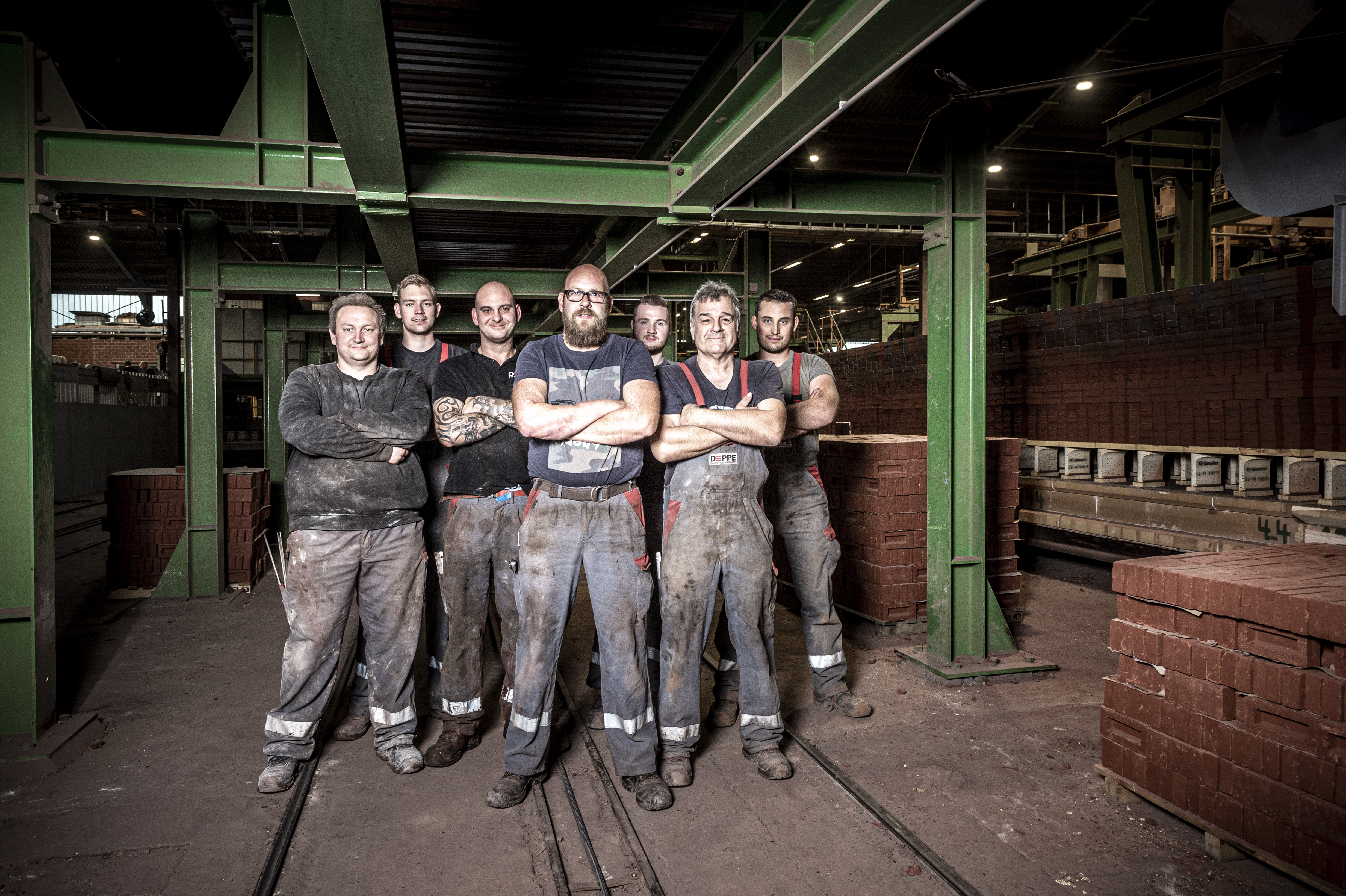
The setting machine
Our freshly pressed bricks contain a lot of water. To prevent them from bursting during the firing process in the kiln, they are dried in our drying chambers, then placed on the kiln car. This cannot be done randomly, but follows very specific schemes depending on the format of the brick and the desired colour variations, ensuring reproducible results.
Ati and Adel are in charge of the setting machine. The loaded kiln car enters the tunnel kiln after setting the bricks. On their journey through the kiln, the bricks pass through a specific firing schedule. In the middle of the tunnel kiln temperatures of up to 1100°C are reached.
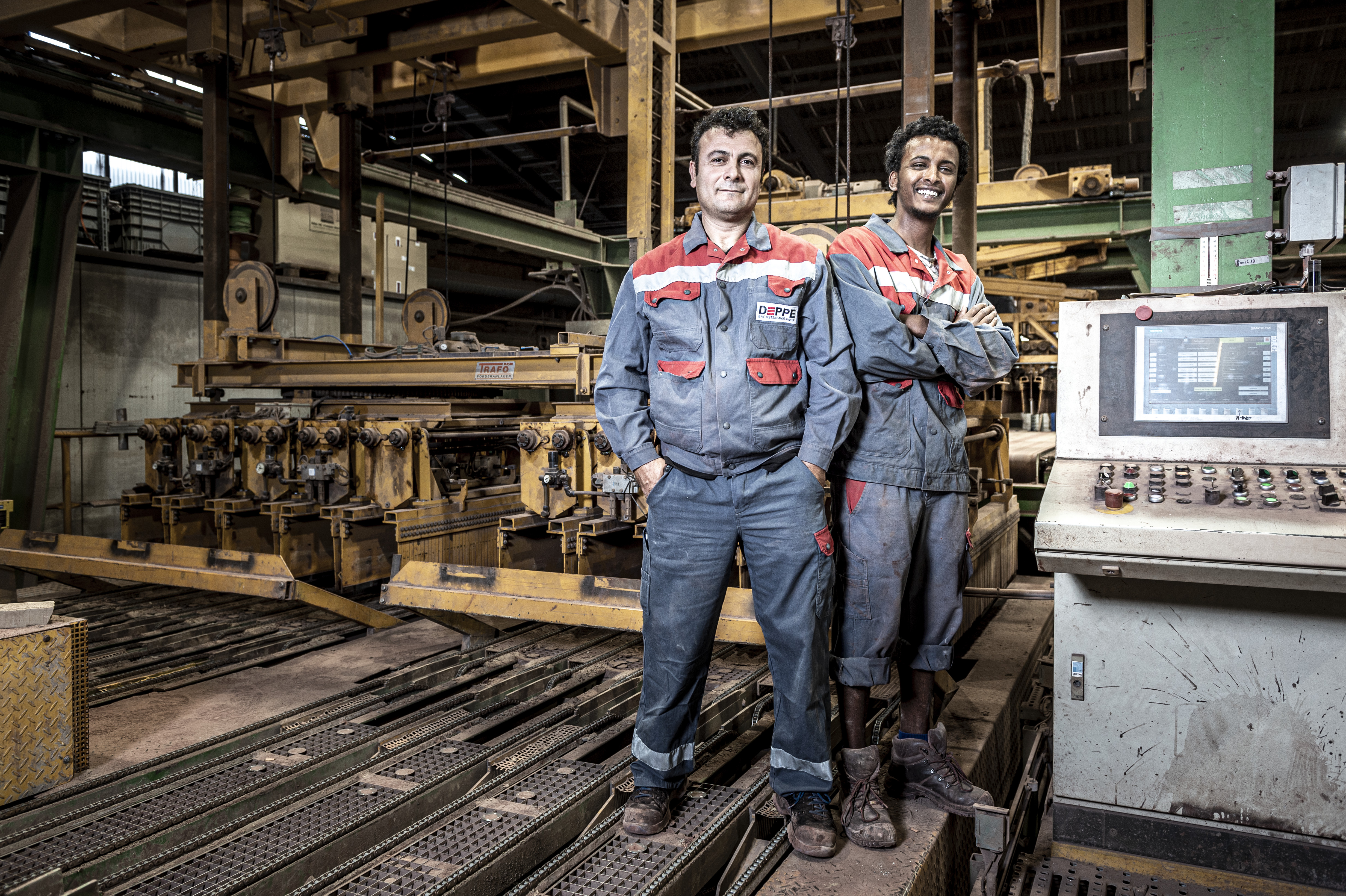
Quality control, sorting, packing and logistics
Every day, about 80,000 bricks leave our kilns. Now things get really busy again and the teams from quality control, sorting and the packing plant, as well as our warehouse staff come into action.
Chris, Björn, Detlef, Jerome, Khaled, Mohammad, Jöris, Gabor, Zibi, Pascal, Ahmad, Jerome, Johnny, Julius, Mudasar and Paul ensure that the production process is completed properly. With packing grippers, the bricks are carefully taken from the kiln car and checked brick by brick. In some cases, special configurations are packed by hand in the big hall. In the end, only quality-checked products, packed on pallets and securely shrink-wrapped, leave our premises and are made ready for dispatch.
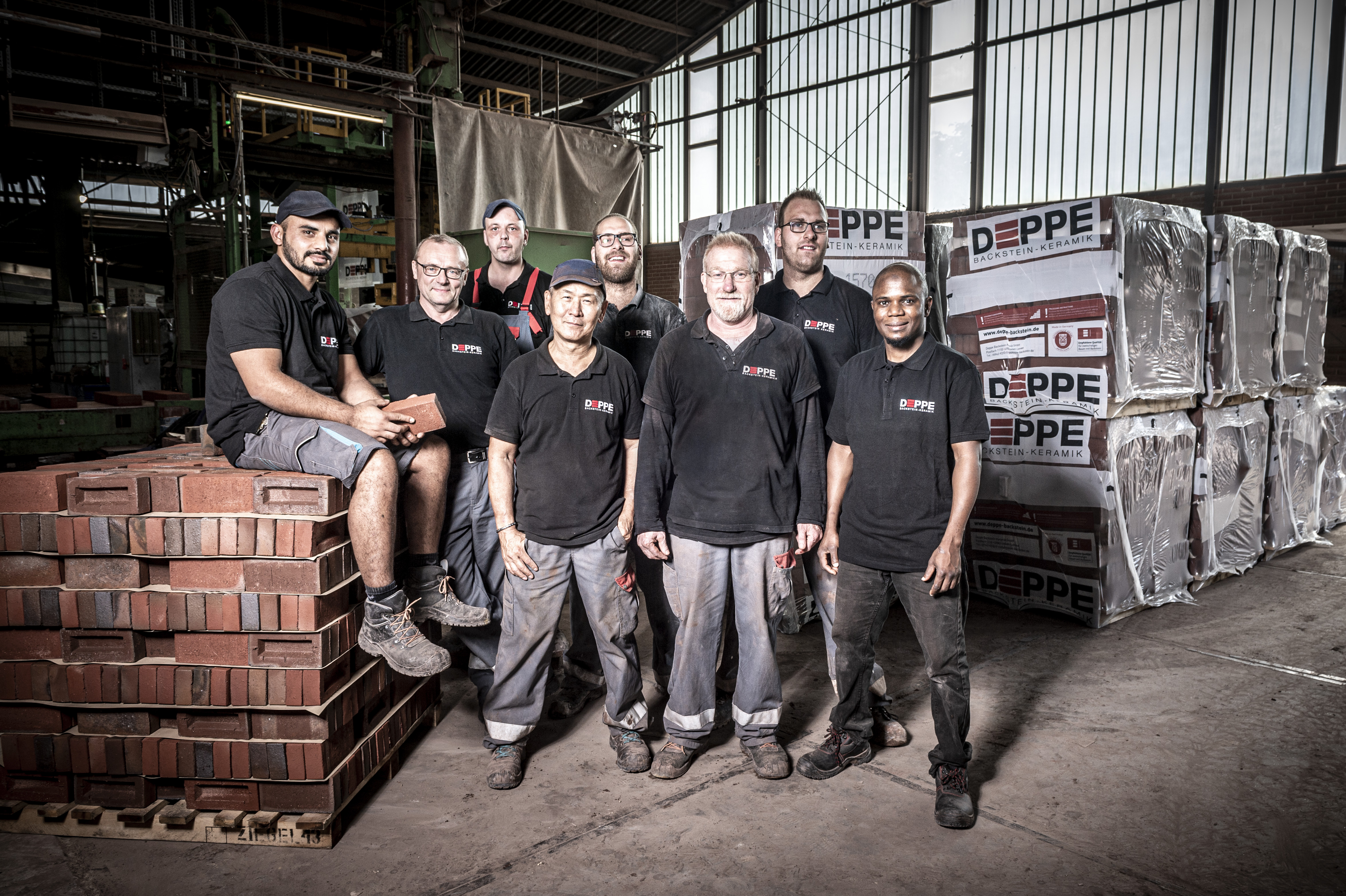
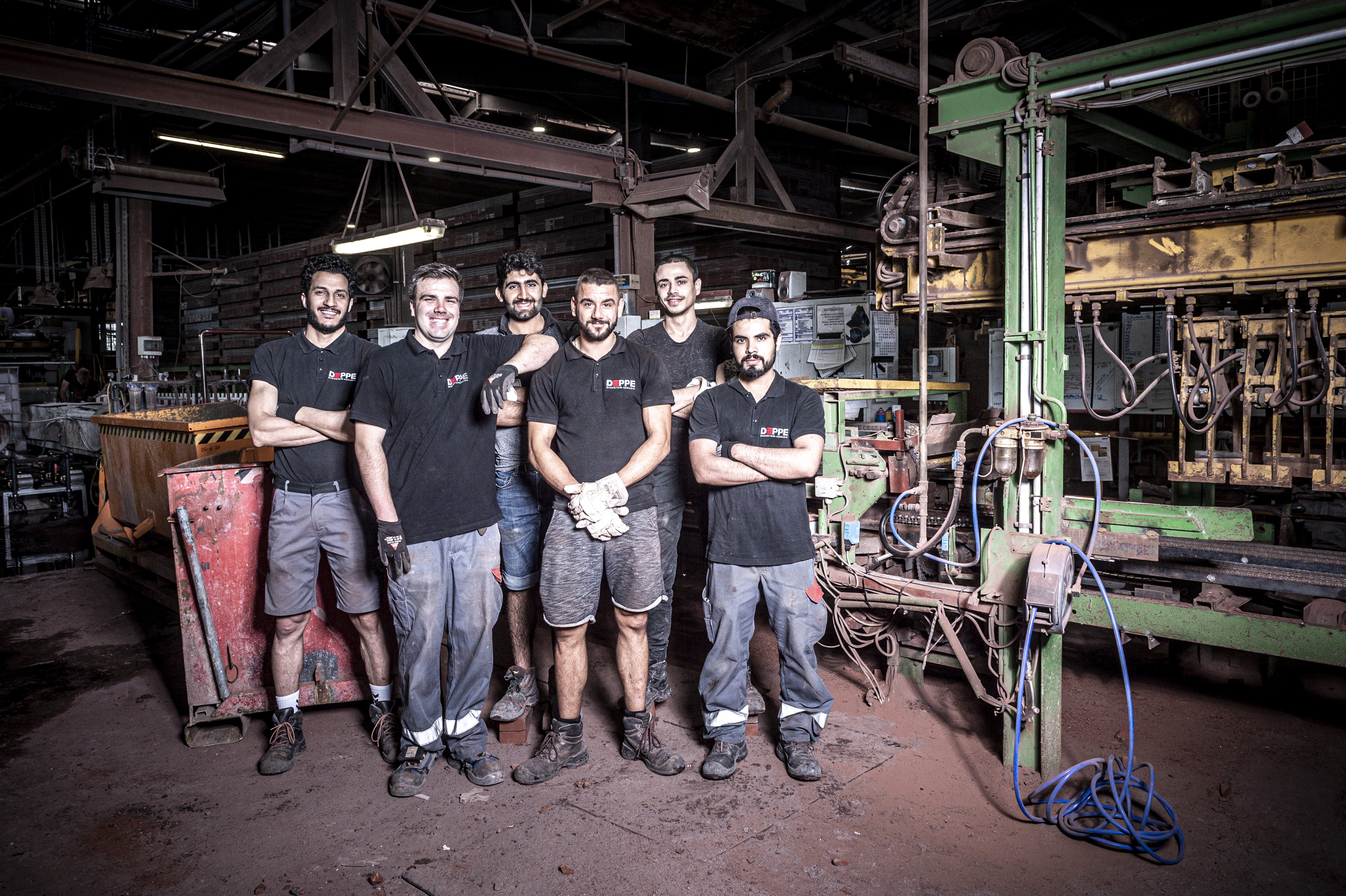
Administration
The team of management, accounting, production planning, marketing as well as office and field staff, admittedly does not look half as exciting/dirty as the rest of the Deppe team in our photo series. But producing bricks is not enough, somebody has to develop, plan, market, sell and manage everything. And Anja, Anna, Benjamin, Benny, Bernd, Branco, Jannik, Jörg, Gina, Heiko, Ingo, Kristin, Lea, Matthias, Tim and of course Dirk do this with full commitment so that we can all continue to manufacture beautiful bricks for appealing architecture.